Heat Printing in Bulk: Maximizing Efficiency for Large Orders
Heat Printing in Bulk: Maximizing Efficiency for Large Orders
In the fast-paced world of printing, efficiency plays a crucial role in determining the success of production processes. Heat printing in bulk requires a well-optimized workflow to ensure high-quality results while minimizing costs and waste. Maximizing efficiency in heat printing production not only enhances profitability but also improves turnaround times, maintains product consistency, and promotes sustainability. In a competitive market, businesses that streamline their operations can better meet customer demands, reduce expenses, and stay ahead of the competition. This blog explores the importance of efficiency in heat printing, the key benefits it brings to production and how to make your business more efficient.
Importance of Heat Printing Efficiency
Efficiency in heat printing is essential for several reasons, directly impacting production quality, cost, and customer satisfaction. Here’s why it matters:
Cost Savings
Efficient processes reduce material waste, lower energy consumption, and minimise labour costs, making production more cost-effective.
Faster Production & Turnaround
Streamlining workflows allows for quicker order fulfilment, helping businesses meet tight deadlines and increasing overall output.
Consistent Quality
Optimized production ensures uniform heat application, reducing the chances of misprints, fading, or defects, which enhances product reliability.
Higher Profit Margins
By reducing waste and improving productivity, businesses can maximize profitability and reinvest in growth opportunities.
Sustainability & Waste Reduction
Efficient heat printing reduces excess ink, vinyl, and paper usage, contributing to environmentally friendly manufacturing practices.
Competitive Advantage
Companies that optimize efficiency can offer competitive pricing, meet customer demands more effectively, and stand out in the industry.
How to Make a Heat Press Business More Efficient
Improving efficiency in a heat press business helps reduce costs, increase productivity, and enhance product quality. Here are key strategies to optimize your operations:
Optimize Workflow and Workstation Layout
Arrange your equipment and materials for easy access. This should minimize unnecessary movement. It's no good spending 5 seconds walking back and forth every time you need to grab a heat transfer to take it to the press. That adds up to 41 minutes of wasted time for every 500 garments you print.
By designating separate areas for printing, cutting, and packing, it streamlines your operation and keeps mess at a minimum. A messy and overcrowded environment is a stressful one, and thats where mistakes happen.
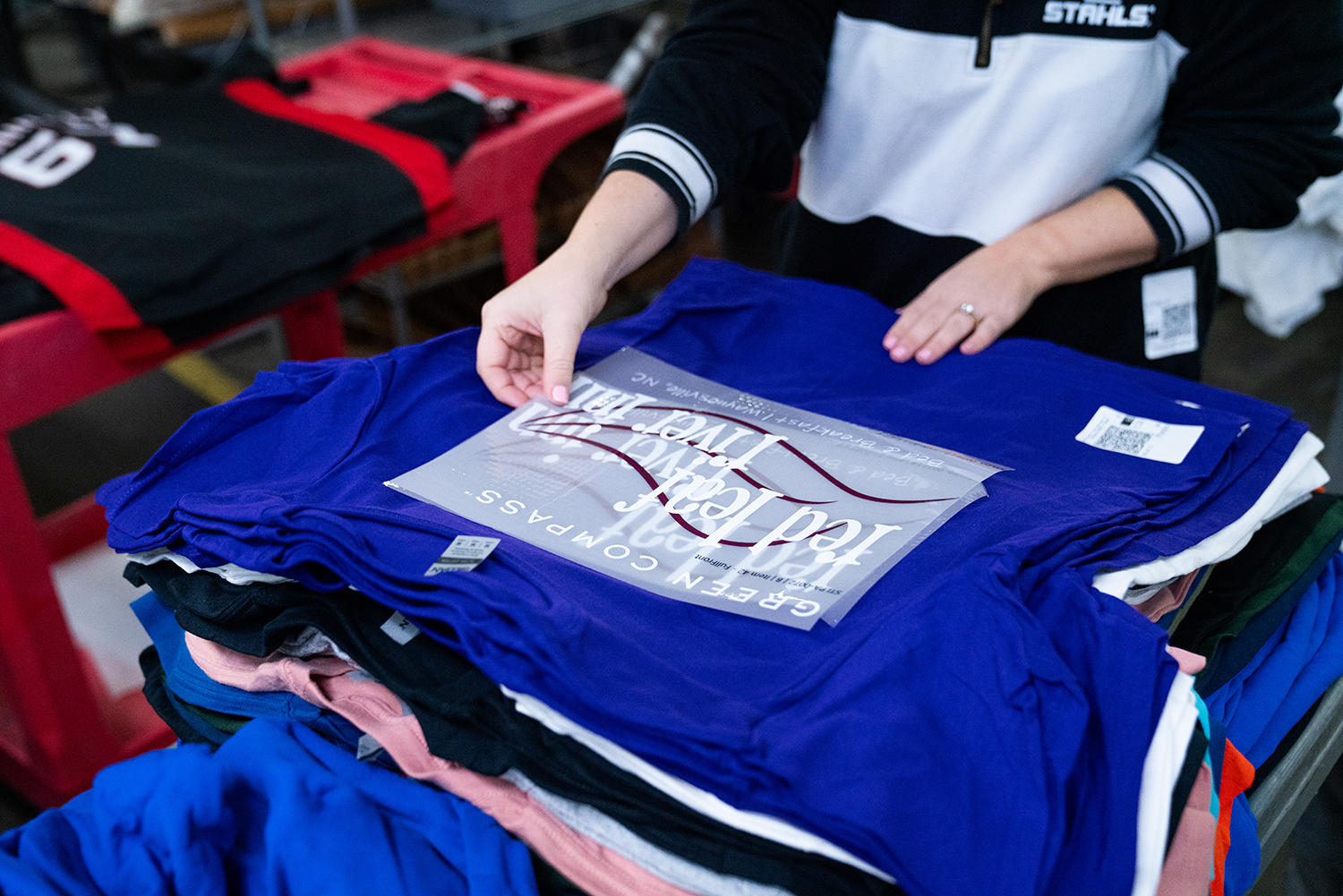
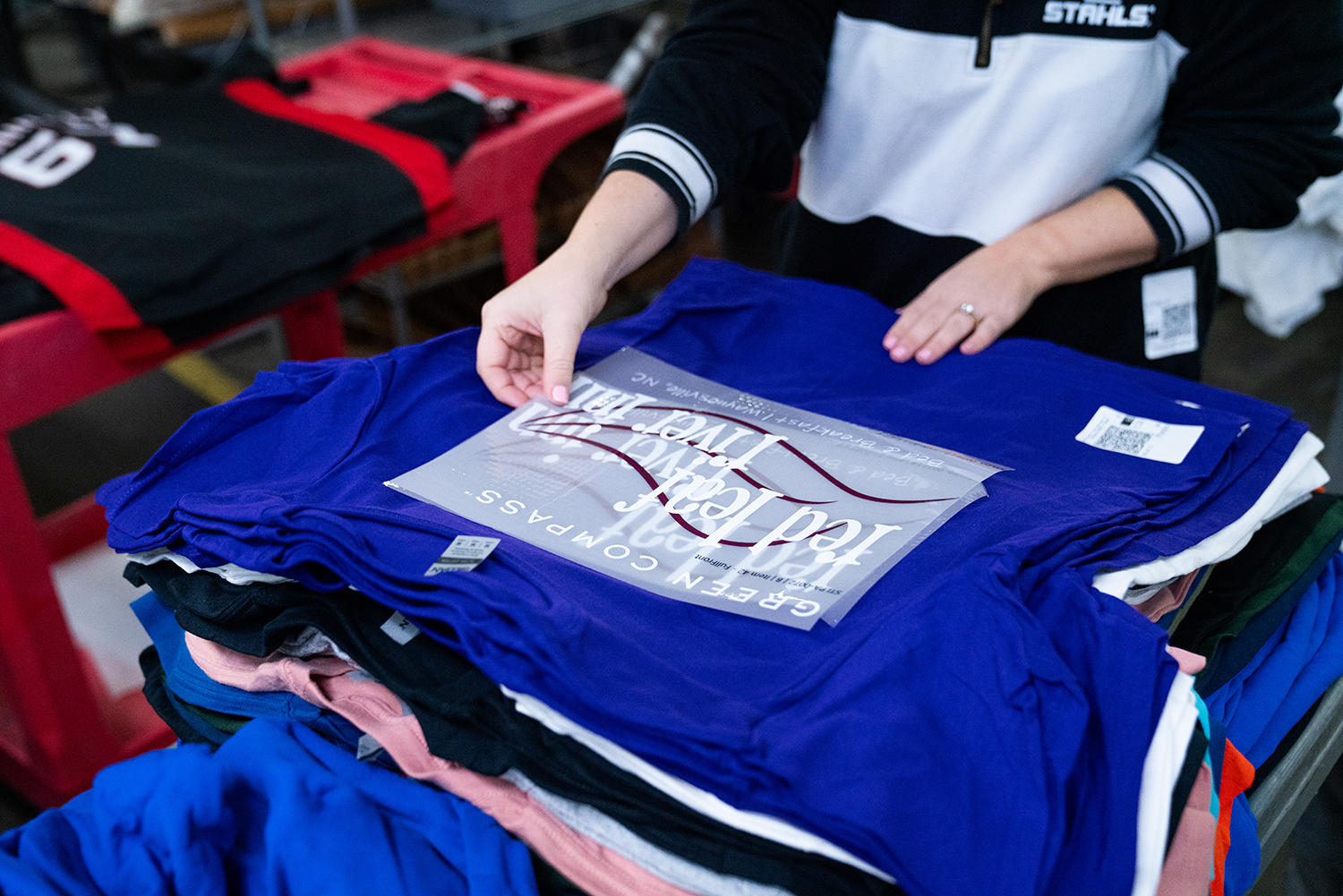
Invest in High-Quality Equipment
Using a reliable heat press with consistent temperature and pressure control is proved to reduce errors. Reduced errors ensure that there are less wasted garments, less wasted materials and less unhappy customers. Hotronix are the World's #1 Heat Press manufacturer and are known for their high quality machines.
Upgrade to automatic or large dual workstation heat press for a higher output with less manual effort. A heat press will reduce user fatigue and scorched garments by opening at the end of it's alloted time. A dual workstation heat press will allow you to prep one garment while fusing the other, ensuring there is a constant flow of printing occuring.
Hotronix offers many auto-release heat presses such as The Auto Open and The Air Fusion IQ. But if you're looking for a dual workstation heat press, you'll need The Dual Air Fusion IQ or The ProPlace IQ. Both offer dual workstations, air-powered press, and auto-release technology but one offers laser alignment and the other, projection alignment.
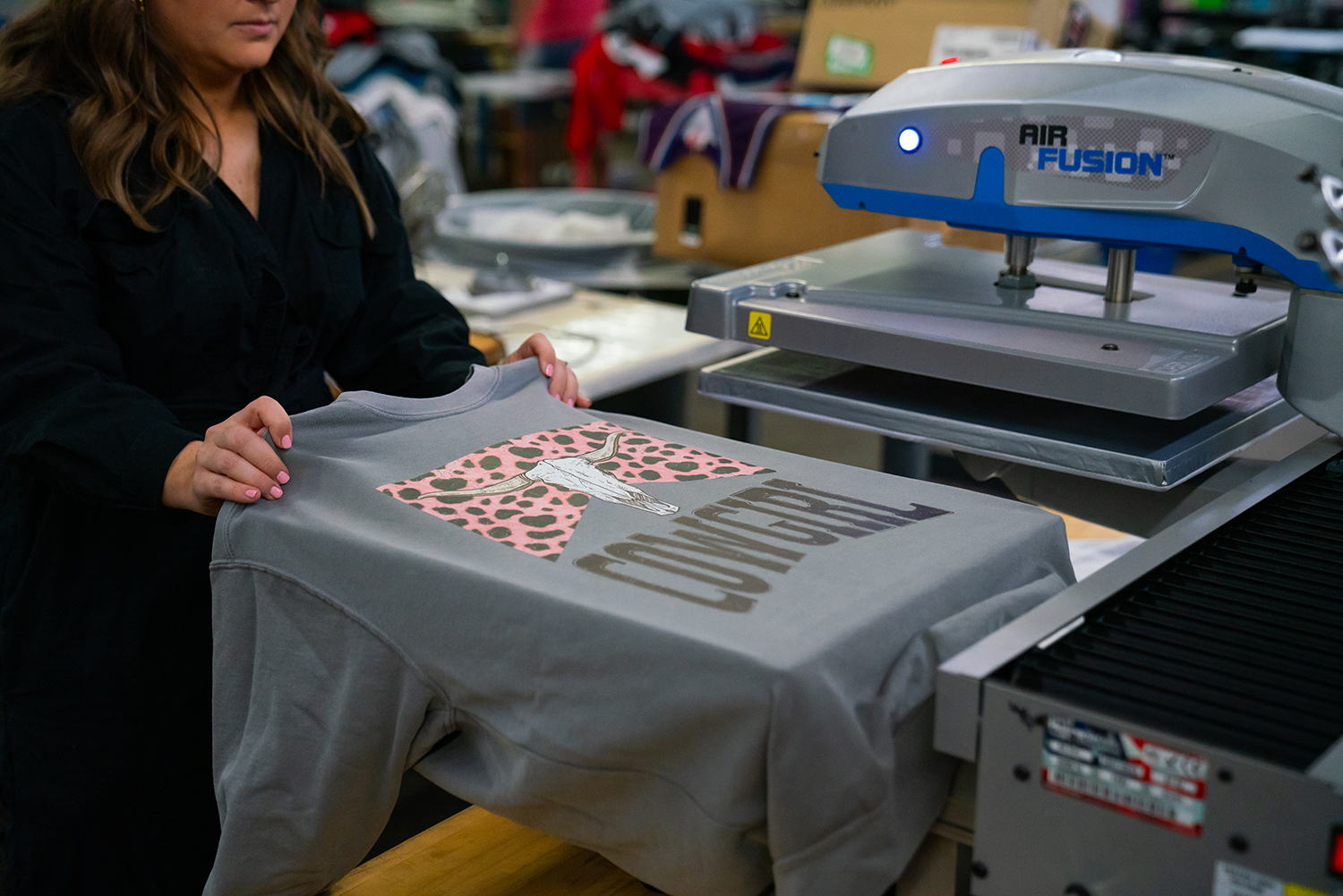
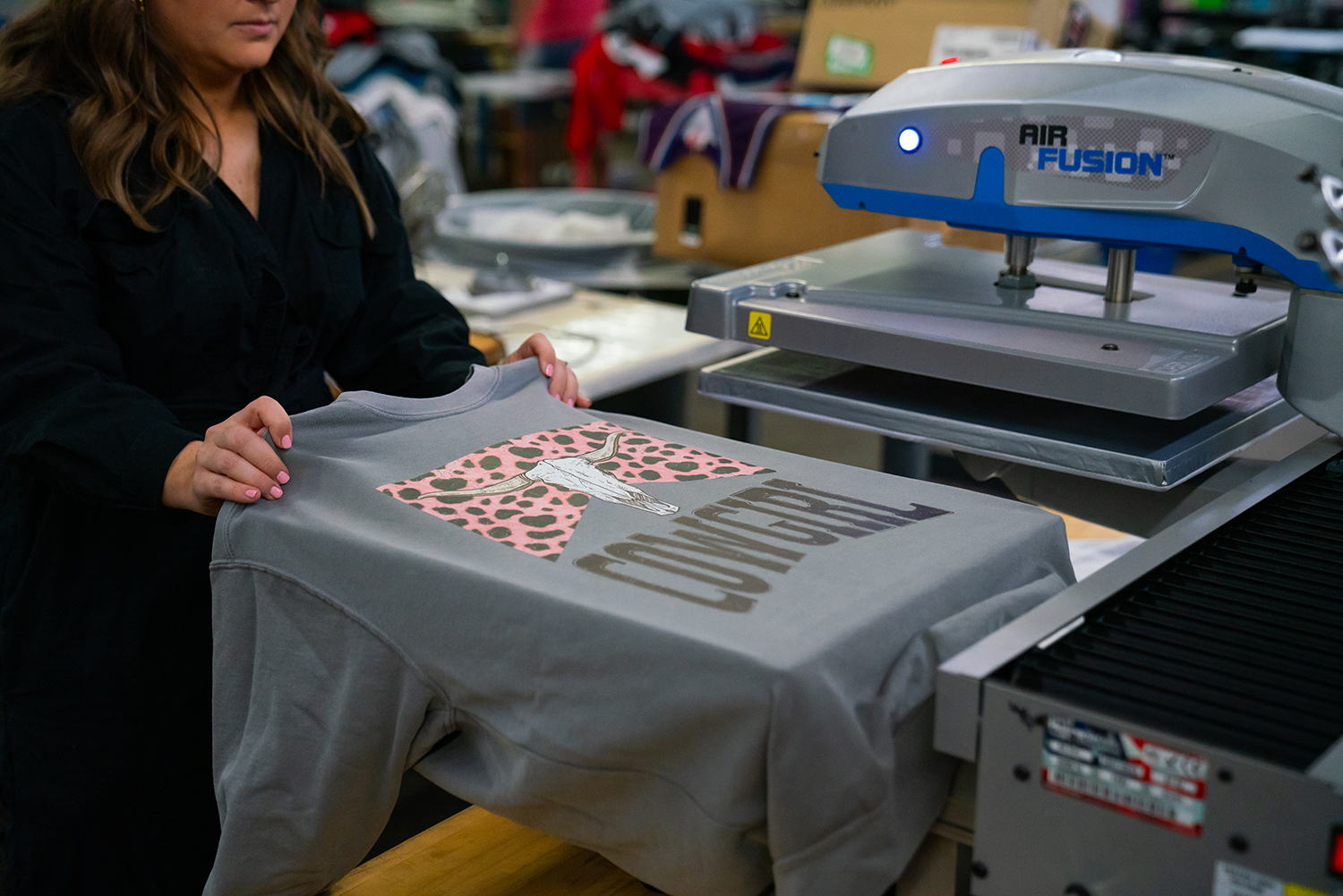
Improve Time Management
Batch similar jobs together to reduce setup times. If you're printing 100 hoodies with 3x placements, print all your back prints at the same time, all your sleeve prints at the same time and all your neck labels at the same time. This minimises the time it takes to change your heat press platen or the accessory that will help you print that placement. If you printed 1 whole garment at a time, you could be spending 5 seconds changing your assisting accessory which equates to over 25 minutes wasted for a small-sized job.
Using a press that has a dual timer will save the user time when adjusting dwell times for each application. Instead of manually changing the seconds for each pre-press and main press, a dual timer will allow you to set a specific time for each fuse.
Automate repetitive tasks where possible. If you can cut HTV on a large gang sheet, this makes much more sense than cutting each design individually. The time it takes to load your htv and set the cutting going will be reduced. Consider switching to custom heat transfers to remove cutting and weeding HTV all together.
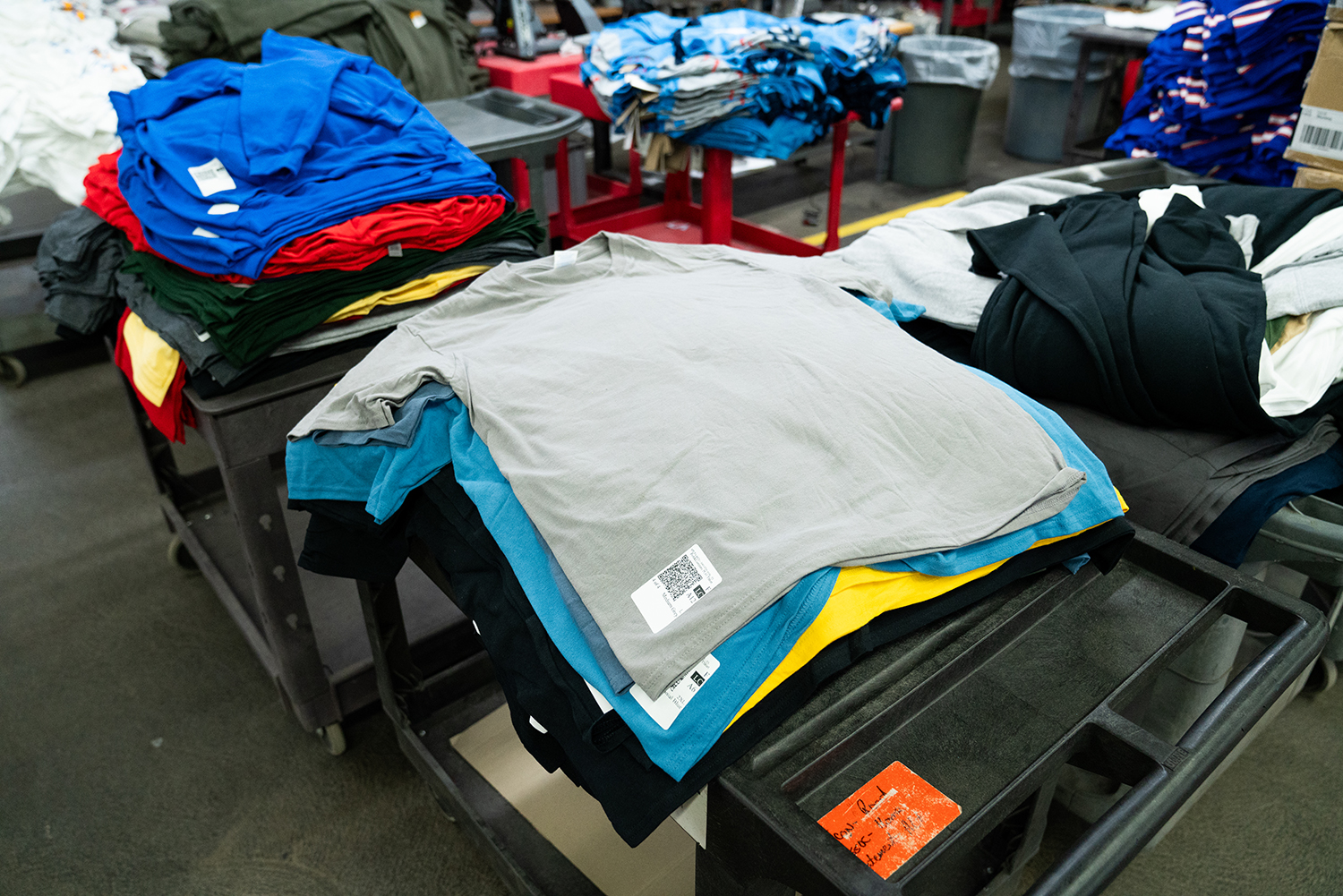
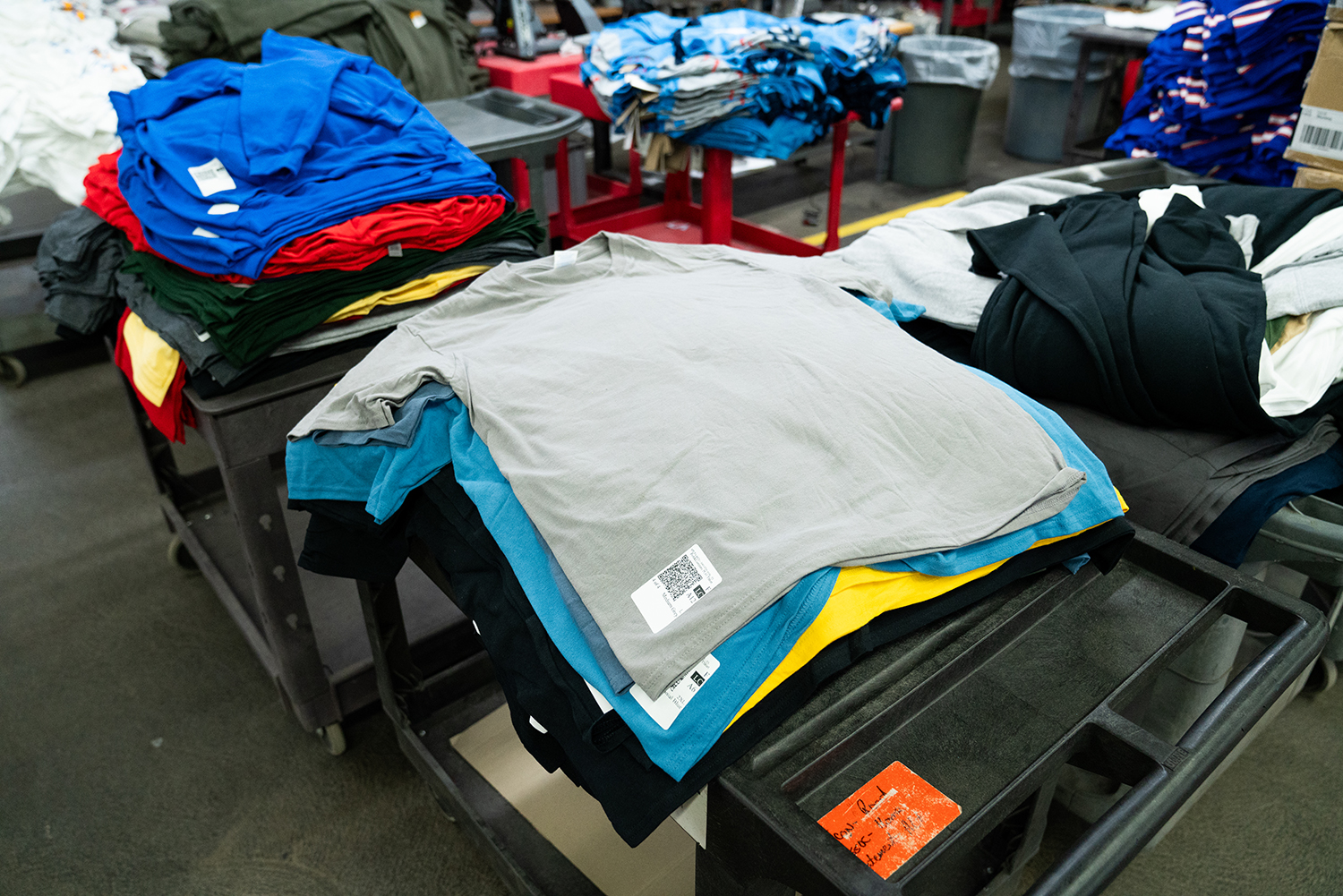
Use High-Quality Materials
Invest in premium materials. Do your research. News flash: A £10 DTF gang sheet from a transfer business that constantly brags about low prices is not going to propell your clothing business to success. In the event that you have an issue with those products, it's likely that the manufacturer will be out of business before you can even complain about their low-quality products.
High-quality products that are proven to work time and time again ensure that you're not delivering disappointing products to your customers, printing reruns, wasting time and eventually, reducing your profits.
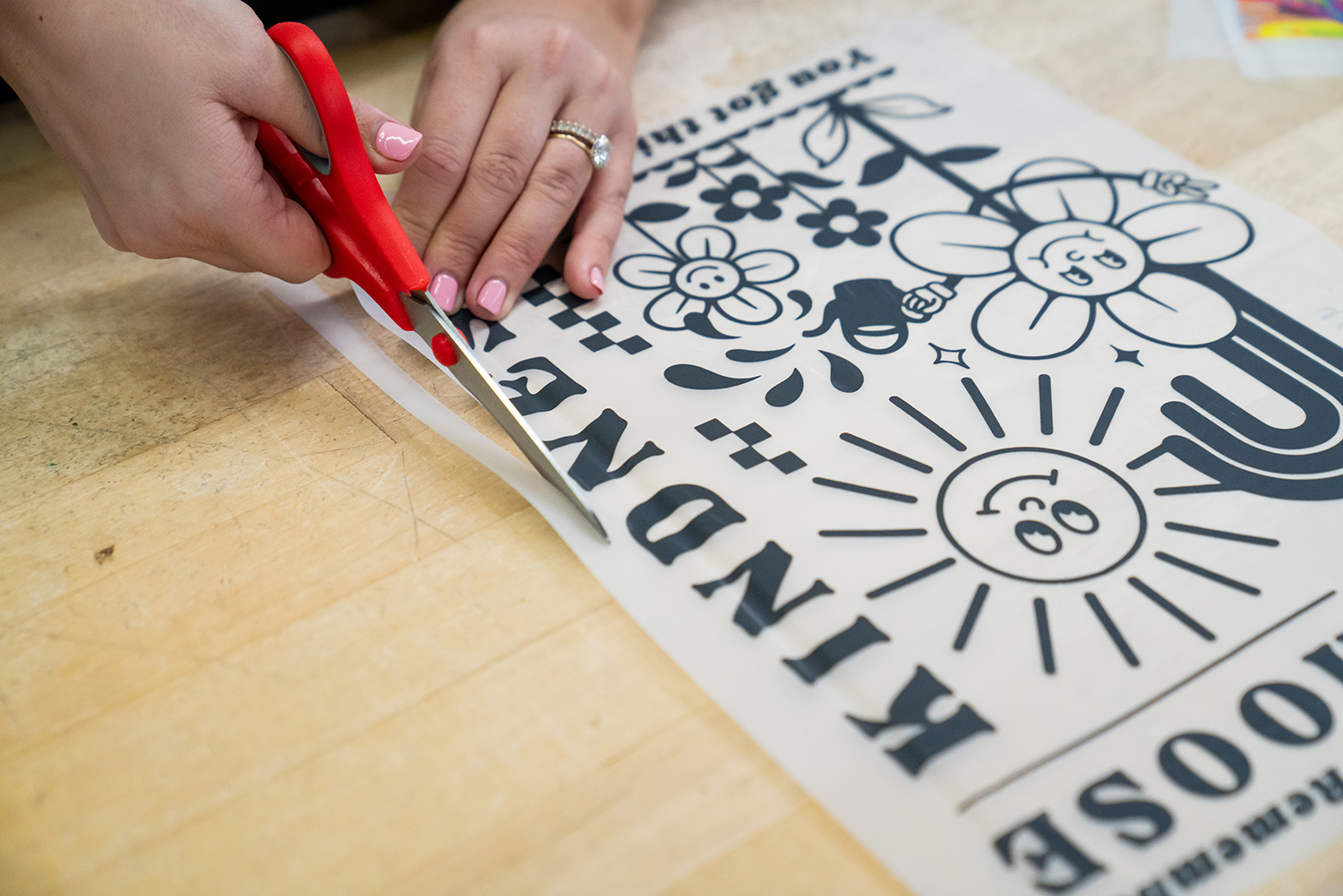
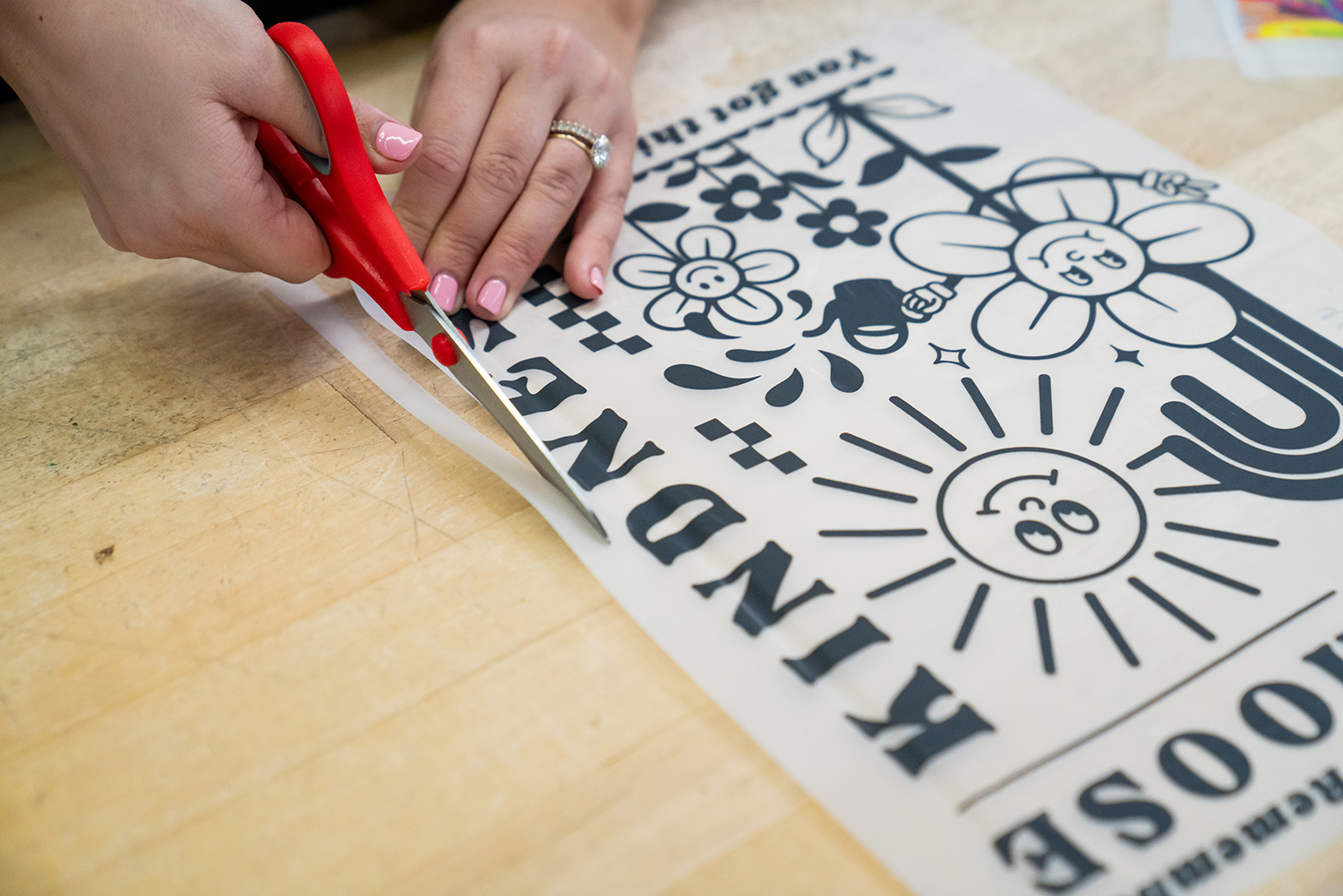
Train Employees and Standardize Processes
Provide proper training on heat press techniques to minimize user errors. You're going to the extent of reading this blog, finessing your production workflow, make sure your employees follow it. Utilising Hotronix heat press features such as the Fusion IQ portal can help you narrow down user errors thanks to the in-depth heat press reports that are generated every time the heat press is used. As an example, if a batch of garments comes back from the customer as faulty, you can check the print logs and see if the user that printed them was using the correct time, temperature and pressure during application.
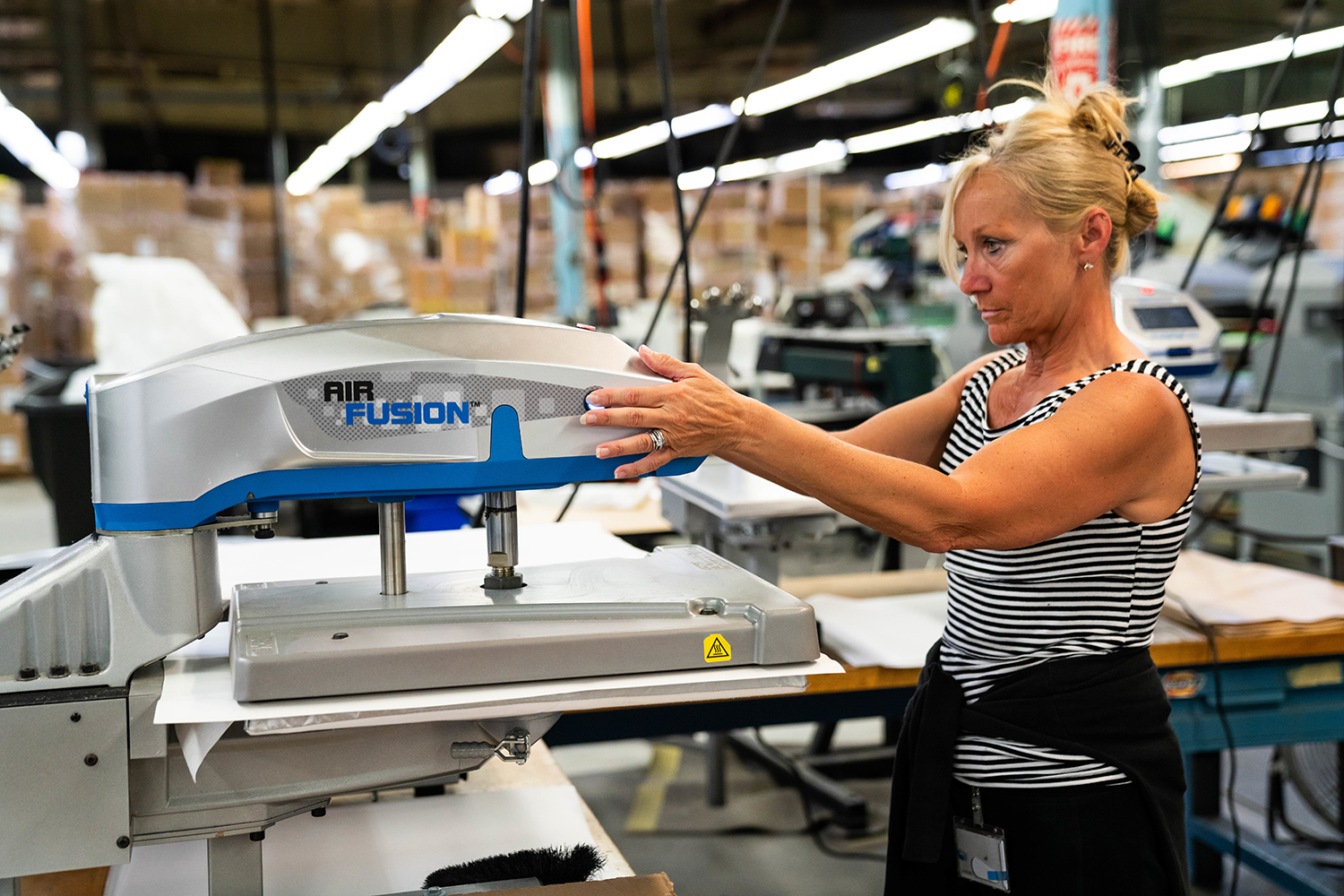
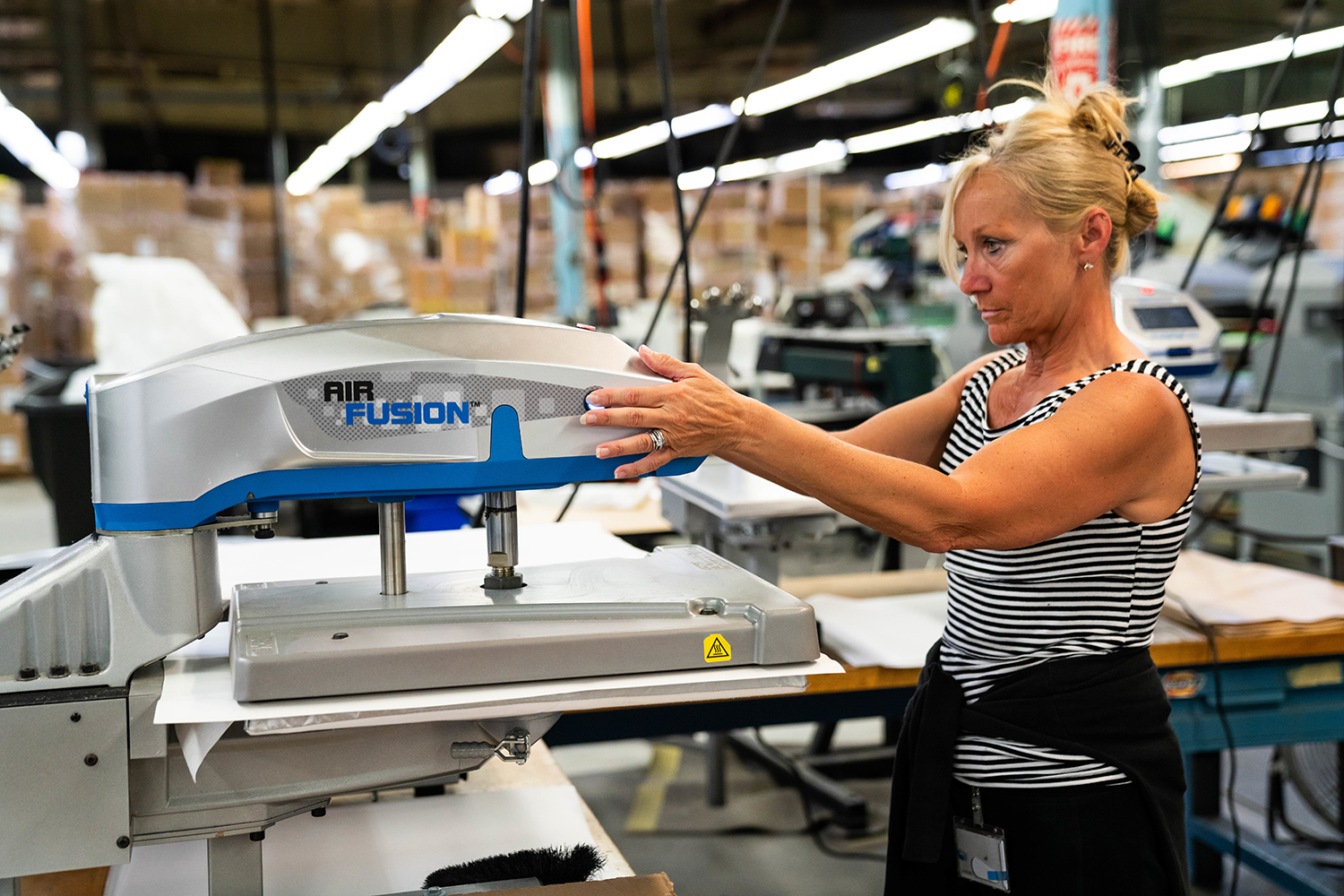
Reduce Waste and Improve Sustainability
Optimize cutting layouts to minimize material waste. Gang sheets allow you to get more for your money whether it's custom heat transfers or HTV. By filling each sheet with as many designs as will fit, you are reducing your cost per design. With that being said, be sure that cutting these designs out is not wasting time on your end. If you're spending too long intricately cutting out each design, this is going to counteract your savings by gang sheeting in the first place.
Using energy-efficient heat presses like the Hotronix Fusion IQ Heat Press range can cut electricity costs as well as time spent waiting for the press to heat up. By utilizing the Fusion IQ portal you can set your heat press to begin heating up 30 minutes before you enter the workshop each day, meaning you're not wasting time waiting for it to come up to temperature. You can also set the presses to go into standby mode after a period of time, again, saving your energy and money.
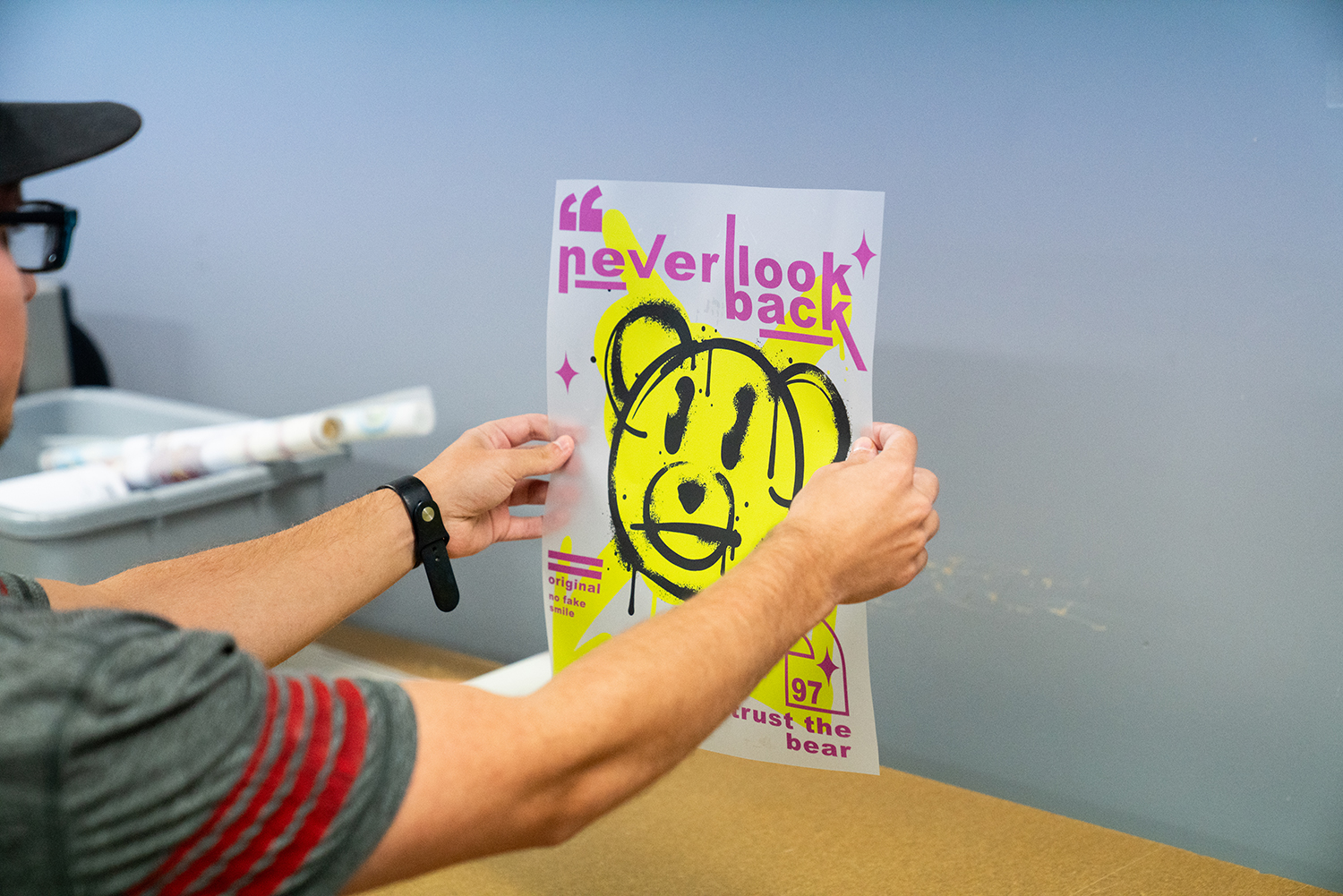
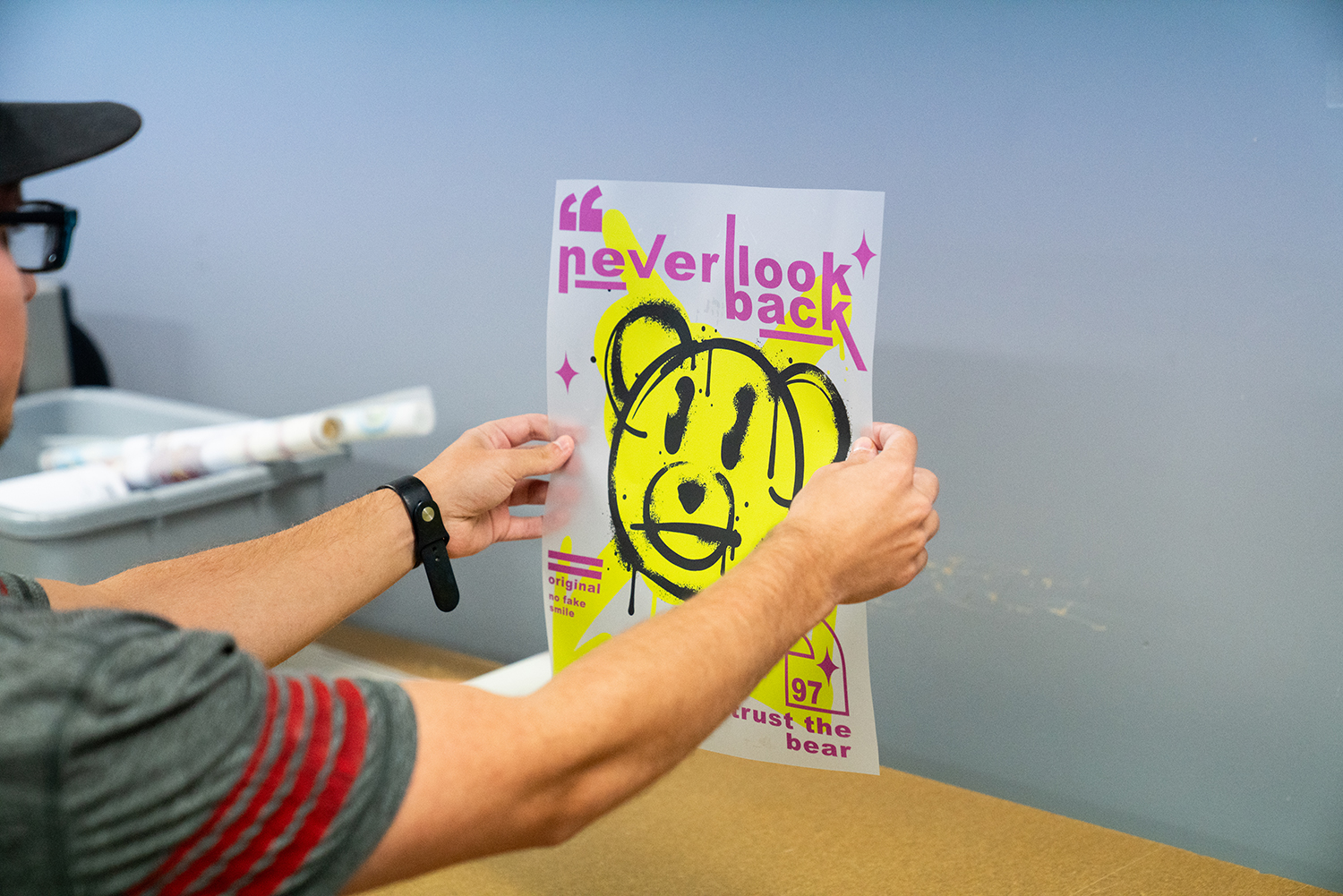
The Big Reveal – 86 Days Back!
If you're looking for a quick win when it comes to saving time for your business, Andy has the perfect video for you.
Printing 500 t-shirts a day with a dual platen heat press and projection alignment means you save 86 out of 250 working days each year. That’s right – 86 days to grow your business, take on more jobs, or even take a well-deserved break.
So, gear up and get those extra days back. With a few smart upgrades and tweaks, you’ll be blazing through t-shirt orders and watching your efficiency soar. Happy printing!
Check out the below video for an a more in-depth explanation: